Authors: Anna Boch, Nicola Neumann, Isabell Roscher, August 31, 2024
1 Definition
The chemical industry is highly globalized and ranks among the three largest industrial sectors in the world.1 With its different segments, the chemical industry has experienced consistent growth since its inception in the 1860s.2 The global chemical industry plays an important role in nearly every manufacturing sector across the globe and have contributed an estimated 5,43 trillion euros to the global economic output in 2022.3 This impact is achieved through direct, indirect and induced effects, supporting around 120 million jobs worldwide. Direct effects come from the chemical industry’s own operations, contributing to GDP (gross domestic product) and directly employing a considerable workforce. Indirect effects result from the economic activity and jobs sustained within the industry’s broad supply chain. Induced effects include the broader economic benefits generated when employees within the industry and its supply chain spend their earnings in sectors such as retail and leisure.4 Of this total, the chemical industry directly employing 10 million people and generates billions of euros in shareholder value and tax revenue for governments.1 In terms of revenue the main markets for the chemical industry are Europe, the United States and Asia. Europe, with Germany, Italy and France as central markets, collectively representing 12% of the chemical consumption. The United States accounts for 15% of this consumption. However, the largest market is Asia, where China and Japan dominate, contributing to a substantial 59% of global chemical consumption.5 In the dynamic market, large multinational companies (MNCs) hold a dominant position in this industry sector, such as BASF, DuPont and Bayer, having maintained their leadership for over a century.6
In general, the chemical industry is a highly diversified sector, characterized by a broad spectrum of processes and products. Despite this diversity, it largely depends on fossil-derived resources such as air, coal, minerals, natural gas, oil and water as raw materials. The chemical industry utilizes these raw materials to manufacture a vast array of more than 60,000 distinct chemical-based products.7 The industry is typically divided into different categories, based on the characteristics of their end products. Smith (2005) identifies three main categories: bulk chemicals, fine chemicals and specialty chemicals.8 Bulk chemicals are generally produced in quantities exceeding 100 million tons annually, such as sulfuric acid, ammonia and ethylene.6 As the chemical products are on the same molecular level, they are mostly undifferentiated and thus the price is the primary competitive factor, leading to narrower profit margins. While bulk chemicals are largely processed further within the industry in order to convert them into more complex products, the fine chemicals are often serve as intermediates for other industries.6,9 Fine chemicals are produced in smaller quantities and are highly purified, but nevertheless, these kinds of chemicals also tend to lack differentiation, making pricing a critical factor.9 Examples for this category are dimethyl formamide, used as a solvent or reaction medium in the manufacture of pharmaceuticals or butyric acid, utilized in flavoring or fragrances.8 Specialty chemicals, which include e.g. pesticides, perfumes or pharmaceuticals, are differentiated and often technologically advanced products. They are often highly tailored and purchased because of their specific functionalities or the perceived benefits they offer.9
Based on the classification of various chemical product categories, the pharmaceutical industry is recognized as an integral part of the chemical industry. According to recent data in 2022 from the American Chemistry Council, pharmaceutical products account for 28% of the global chemical shipments.5 The pharmaceutical industry’s global turnover of 1,95 trillion euros increase the total turnover of the chemical-pharmaceutical industry to 7,38 trillion euros.3While profitability remains a key objective, an equally critical goal is to support healthcare systems by ensuring that essential medicines are available at the required time and place.10 The pharmaceutical industry is responsible for the production, distribution and consumption of drugs.
The products are typically categorized into two groups: prescription medications and self-medications. Prescription medications are shared with healthcare providers through the efforts of medical sales representatives and through marketing in professional medical journals. On the other hand, only over-the-counter medications, which are approved for self-medication, can be sold directly to consumer and advertised to the general public.11 The development of new pharmaceuticals is a highly resource-intensive and protracted process, encompassing a series of sequential phases, from discovery through regulatory approval to market launch.12 The resulting high costs are largely driven by substantial expenditures on research and development (R&D). Compared to the broader chemicals manufacturing industry, the pharmaceutical industry is considered one of the most research-intensive sectors.11 In 2022, the pharmaceutical industry research and development in Europe amounted to 47.010 million euros, making it the most R&D sector in Europe with an intensity of 12,9%.13,14 In comparison, industries such as automotive and aerospace have significantly lower R&D intensities, at 4,8% and 4,5% respectively.14 In addition to the developing the product itself, the production process for new pharmaceuticals must also be established to secure final approval from regulatory agencies.12 In this context, pharmaceuticals as specialty chemicals, require both product and process development to adhere strict regulatory guidelines established by agencies like the EMA (European Medicines Agency) or the FDA (Food and Drug Administration).9
The chemical-pharmaceutical industry as a whole and their products and use of chemicals are relevant prerequisites for economic development in all countries. Chemicals, in various forms, have a direct or indirect impact on everyone, playing a crucial role in food production (fertilizers, pesticides, food additives, packing), healthcare (pharmaceuticals, cleaning materials) and overall quality of life (appliance, fuels).15
2 Sustainability Impact and Measurement
The chemical-pharmaceutical industry is a strategic industrial sector and has been a key driver of economic growth and wealth creation over the last two centuries.16 While the extensive use of chemical has contributed to improving urban living standards, it has also led to adverse sustainability impact.17,18 By 2030, this industry is projected to experienced rapid growth, with per capita production excepted to double compared to level from 1990, further emphasizing the importance of addressing sustainability challenges.16 According to the principle of the triple bottom line, the chemical-pharmaceutical industry plays an essential role in driving all three dimensions of sustainability – environmental, social and economic.19
2.1 Environmental Dimension
The environmental dimension of the chemical-pharmaceutical relates to how its processes, products and services impact the environment.20 The chemical-pharmaceutical industry’s impact on climate change is assessed through the measurement of greenhouse gas (GHG) emissions, including CO2-emissions.21 The chemical-pharmaceutical industry accounts for 7% of global industrial GHG emissions and therefore, according to the definition of the chemical reaction thermodynamics, the industry is one of the highest CO2 generating industries in the world.18,22 Figure 1 shows the direct CO2-emissions by industry worldwide in 2022. Leading the emissions are the oil industry, which accounts for 55%, followed by the iron and steel industry at 13%, and the cement industry at 12%.23 Within industry, the chemical-pharmaceutical industry ranks as the fourth-largest producer of CO2-emissions among global industries, highlighting a significant need for action to meet the objectives of the Sustainable Development Goal (SDG) 13: Combat climate change and reduce its impact.23,24
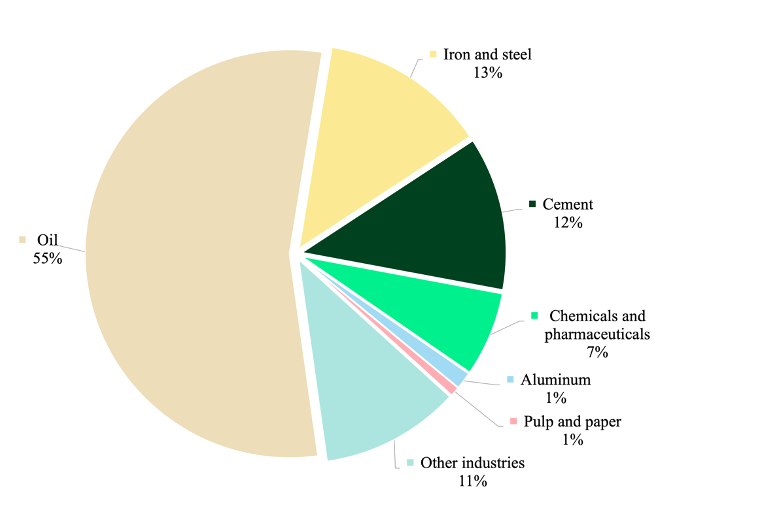
Especially pharmaceutical chemicals, given their complexity and high value-added nature, typically leave a larger environmental footprint per kilogram compared to bulk chemicals. This is primarily due to the complex chemistry involved in producing active pharmaceutical ingredients (APIs), which requires advanced multistep manufacturing processes.25 An immediate and concerning observation is that the pharmaceutical sector is not environmentally sustainable. In 2015, its emissions intensity was roughly 55% higher than that of the automotive sector.26
The sustainability performance of the chemical-pharmaceutical industry is also influenced by the high energy demand associated with these complex manufacturing processes. In 2019, the chemical industry ranked as the third-largest consumer of industrial energy, following the cement and iron and steel industries in terms of oil and gas usage. Today, the chemical industry has become the leading industrial energy consumer worldwide. This shift is primarily driven by the high use of fossil fuels as feedstocks, where a substantial portion of fossil carbon is incorporated into the produced chemicals.27
Beyond energy use, the industry is a major water consumer, and its processes generate substantial hazardous and solid water.28 These wastes include solvent water and toxic residues that, if not properly managed, contributes further to the industry’s CO2-emissions and pose significantly environmental risks.29 In the context of waste issue, research indicates that the disposal of unused pharmaceuticals alone could add an estimated 23,000 to 105,000 metric tons of CO2-emissions annually.30 This trend in waste generation is mirrored in the United States. As shown in Figure 2, different industry sectors have managed varying amounts of chemical waste between 2013 and 2022.31
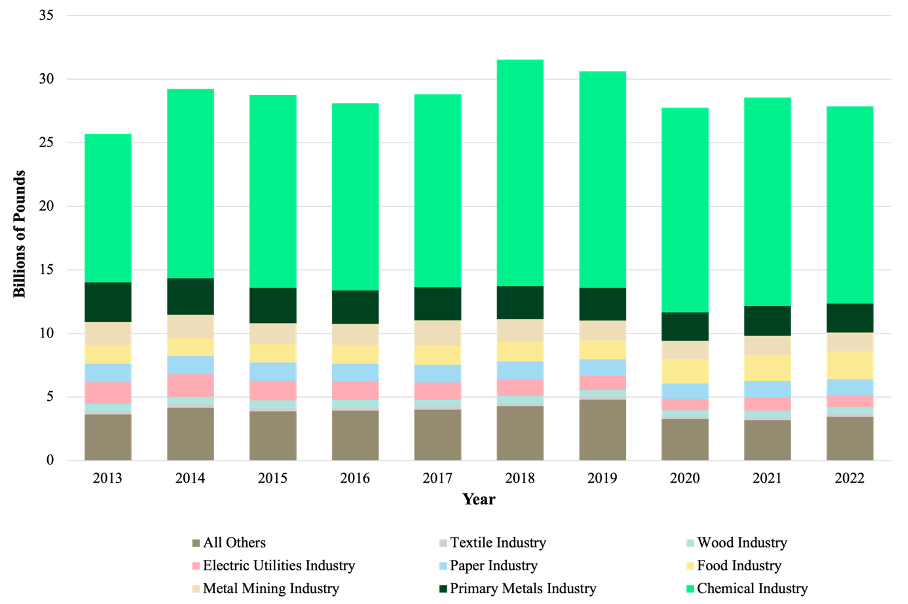
The volume of waste handled by these sectors has evolved over the years, with significant changes observed in the chemical manufacturing sector. In 2013, this sector was responsible for managing 44% of all waste, which rose to 54% by 2022. The chemical industry is extensive, encompassing a wide range of product-producing industries that heavily rely on chemical usage for their operations.32 Consequently, the chemical-pharmaceutical industry is confronted with the challenge of creating greener manufacturing processes by enhancing resource efficiency, supporting global sustainability, and driving the circular economy forward.33
2.2 Social Dimension
As important as the environmental dimension, the social dimension is fundamental to achieving sustainability, functioning as a vital measure of the chemical-pharmaceutical industry’s impact on social well-being and public health.34 Chemical hazards arise during chemical synthesis, manufacturing, processing and transportation, leading to numerous environmental impacts that also can affect human health. A chemical hazard refers to a workplace risk that stems from contact with harmful chemicals. This exposure can trigger a variety of health issues, both in the short term and over an extended period. The types of hazardous chemicals are diverse, including asthma genes, carcinogens, dermatologic agents, immune agents, neurotoxins, pneumoconiotic agents, reproductive toxins, sensitizers and systemic toxins.1 In comparison to the early 20th century, there has been a notable expansion in the number of facilities that manage hazardous chemicals globally, mainly due to the diversification of products and industrial activities. Furthermore, these facilities are now often situated closer to one another and to densely populated areas as a result of growing population densities. While effective safety protocols can readily reduce minor incidents like first-aid cases, lost time injuries and isolated fatalities, preventing large-scale accidents with multiple casualties is significantly more difficult. Unfortunately, the global trend shows that both the occurrence and severity of these major accidents have been on the rise.35 Despite the global increase in the number of facilities managing hazardous chemicals and the associated risks, a positive trend can be observed in the EU regarding the production of the most hazardous chemicals – those classified as carcinogenic, mutagenic, and reprotoxic. Between 2004 and 2022, the production of these dangerous substances decreased from 42 million tons to 36 million tons, indicating progress in reducing the volume of these high-risk chemicals.36
In order to leverage chemistry as an important driver of sustainable development, gender equality as outlined in the SDG 5 must also be urgently addressed.37 The chemical industry, dominated by large-multinational companies, still faces the challenge in achieving gender parity, particularly in top management where women remain underrepresented.37,38 In 2016, women occupied 16.7% of the 430 board director roles and 14.2% of the 402 executive positions across 42 major U.S. chemical firms. In contrast, within the 13 largest European companies, their representation was greater in supervisory roles, with women holding 28.6% of the 154 board seats, but their presence in executive positions was lower, at just 10%.38 A similar distribution is evident at BASF, the largest MNC of chemistry, where women constitute 28.4% of the top management.39 The pharmaceutical industry as part of the Human & Health sector stands out for its more balanced gender representation compared to other key industries. In 2016, 46% on average of the pharmaceutical workforce across the EU were women. This rate is nearly double that of automotive manufacturing at 24% and three times higher than in aerospace at 16%.40 Reflecting this trend, one of the leading pharmaceutical companies Bayer reports a women’s employment rate of 41,1% among its 100.000 employees, with 31,8% representation in top-management out of total of 556 managers.41 This comparison underscores the significant gender gap still present in the chemical industry, particularly when contrasted with the more balanced representation found in the pharmaceutical sector. Without equal representation in the chemical-pharmaceutical industry, there is a greater risk that gender-related issues and perspectives will be systematically ignored.38
2.3 Economic Dimension
Finally, the economic dimension of sustainability is also important within chemical-pharmaceutical industry. According to the Global Reporting Initiative (GRI), economic sustainability encompasses the effects a company has on its stakeholders and the broader economy. However, there is also an internal perspective, which consider how company’s economic sustainability affects its financial health and performance.20 Economic sustainability in the chemical-pharmaceutical sector is contingent upon a complex interplay of multiple interrelated factors. The chemical-pharmaceutical industry relies on non-renewable resources, particularly fossil fuels, for both energy and as raw materials.7 This dependence creates economic vulnerabilities, as fluctuations in fossil fuel prices can lead to increased production costs and economic instability.42 Additionally, the industry’s substantial carbon footprint and its reliance on finite resources pose long-term risks to economic sustainability as global pressures for decarbonization.22,43
In addition to resource management, economic sustainability in the chemical-pharmaceutical industry is also challenged by strategic decisions around patent acquisition and automation. The reliance on patent acquisition and automation as primary strategies for economic sustainability can lead to inefficiencies within the industry. For example, focusing heavily on process patents rather than product innovation may limit the industry’s ability to adapt to changing market demands and technological advancements. Furthermore, as Azad et al. (2018) suggest, scale inefficiencies often outweigh the benefits of technical efficiency, indicating that a narrow focus on these strategies can hinder the overall economic resilience of large pharmaceutical companies.44
Moreover, strategic approaches within the healthcare systems, as highlighted by Aquino et al. (2018), often prioritize cost control and sustainability. This focus on reducing costs can lead to the consequence of cutting services instead of improving efficiency or minimizing waste. Additionally, attempts to boost efficiency are frequently reduced to standardizing processes through the implementation of protocols and service delivery standards, which may restrict innovation and compromise the quality of care.45
Another important factor influencing economic sustainability in the chemical-pharmaceutical industry is the impact of regulatory compliance.12 As governments and international bodies impose stricter environmental and safety regulations, companies face rising costs associated with compliance. While these regulations are essential for mitigating environmental damage and protecting public health, they can create economic challenges, particularly for smaller firms that may struggle with the financial burden.46 This pressure can lead to industry consolidation, reducing competition and potentially increasing costs for consumers.47
While all three dimensions – environment, social and economic – are essential for advancing sustainability, attempting to balance these elements often results in subpar outcomes. The real long-term objective should be to ensure that these three dimension operate in a synergistic manner, mutually reinforcing one another.48 As a reaction to the challenges posed by the chemical-pharmaceutical industry, the Rio Declaration within Agenda 21, called for intensified research to develop safer alternatives to persistent chemicals. This response laid the foundation for the emergence of Green Chemistry in the 1990s, a progressive approach focused on reducing waste, lowering energy consumption and enhancing safety for both environment and workers.49
3 Sustainability Strategies and Measures
Over the past decade, a discernible transformation in perspective has been observed within the chemical and pharmaceutical industry. There has been a notable shift in emphasis from traditional concepts that prioritize chemical yield to an alternative, cleaner chemistry that assigns value to the maximization of raw materials utilization, the elimination of waste and the avoidance of the use of toxic and hazardous substances.50
3.1 Green Chemistry
Green Chemistry (GC) represents a non-regulatory, economically driven approach to sustainability, which can be employed as a basis for the assessment of chemical processes at the conceptual and design stage.48,51 It encompasses the design and development of chemical products and processes with the objective of reducing or eliminating the use and generation of substances that are hazardous to human health and the environment. The twelve principles of GC serve as a comprehensive framework for the design of novel chemical products and processes, encompassing all stages of the process life cycle, from raw materials used to the efficiency and safety of the transformation, the toxicity and biodegradability of the products and reagents employed.52 One of the fundamental tenets of GC is the elimination of solvents in chemical processes, or the substitution of hazardous solvents with environmentally benign alternatives such as water, fluorous and ionic liquids.53 Furthermore, the GC principles emphasize the minimization of energy requirements of chemical processes as well as the potential for accidents due to substances used in a chemical process. Additionally, the GC principles encourage atom economy, the reduction of chemical derivatives, the use of renewable feedstocks and the real-time analysis for pollution prevention. Moreover, the GC principles encompass guidelines regarding product design. These guidelines stipulate that chemical products should be designed in such a way that their intended function is fulfilled while their toxicity is minimized. The design of chemical products should also take into account their ability to deteriorate once they have completed their intended purpose, preventing the persistence of such substances in the environment.51 The pharmaceutical and biotechnology group Pfizer provides an illustrative case study for the implementation of GC principles. The company has demonstrated a robust commitment to integrating GC principles into its research and development processes, as well as retroactively incorporating these principles into existing Pfizer products.54 For example, in accordance with the GC principle of utilizing safer solvents in chemical processes, Pfizer has developed a solvent selection tool that classifies solvents into groups based on their nature and subsequently ranks them according to criteria including worker safety, process safety, and environmental and regulatory considerations. This method facilitates the straightforward identification of solvent alternatives that are deemed to be more environmentally friendly. Following the implementation of this solvent scoring method, Pfizer reported a 50% reduction in the use of chlorinated solvents across their entire R&D division between 2004 and 2006.55
The implementation of GC principles can enhance the performance, capabilities and efficiencies of the products and processes to which they are applied, while simultaneously addressing environmental and human health concerns. Research demonstrates that the principles can facilitate the achievement of synergistic outcomes between environmental stewardship, economic prosperity and social responsibility by designing in sustainability at the molecular level.48Nevertheless, there is a potential issue with applying only one or a subset of the twelve GC principles, as this can result in counterproductive outcomes and even lead to nonsensical results. Furthermore, some of the principles may be in direct contradiction with one another, thereby rendering it challenging to ascertain the most efficacious course of action for achieving the optimal overall result. To illustrate, an increase in yield or a reduction in waste may result in higher energy consumption.56 In order to circumvent the double economic penalty associated with the generation of waste (namely, the expenditure incurred on the procurement of chemicals that are ultimately not converted into a product, coupled with the costs associated with their disposal), it is imperative that the GC principles are integrated into the initial stages of product development.48
Additionally, the twelve principles of GC are qualitative in nature and do not provide clear metrics for measurement. Consequently, a series of straightforward metrics were devised, based on the twelve principles. The most renowned and widely utilized metric for gauging the environmental impact of a chemical process is the E-Factor. The E-Factor, defined as the mass ratio of waste to the desired product, incorporates losses of reagents and solvents. Due to its success in tracking diffusion, it was benchmarked in the chemical industry.56 Another green metric, the process mass intensity (PMI), offers a more comprehensive evaluation of the mass necessities of a process, encompassing synthesis, purification, and isolation. Defined as the ratio of the total mass of materials used in a process to the mass of the desired product, the PMI is directly related to the E-Factor. In contrast to the E-Factor, which assesses the waste generated by each synthesis process, the PMI evaluates the catalyst, solvent, and reagents utilized in each synthesis process. It should be acknowledged that the PMI does not account for the environmental impact incurred during the manufacture of starting building blocks and reagents nor does it consider factors such as energy usage, logistics or the complexity of the starting materials. However, as a result of its focus on value and efficiency, the PMI was identified as the principal mass-related green chemistry metric and as an indispensable indicator of the overall greenness of a process.57 In regard to the GC metrics, it can be concluded that the most significant challenge is to develop metrics that account for the diversity of the twelve GC principles while maintaining ease of use. In order for GC metrics to serve as effective decision-making and motivational tools, it is essential that they consider all of the synergistic elements of sustainability: environmental responsibility, economic prosperity, and social responsibility.48
3.2 Biocatalysis
One principle of GC has been designed with the specific objective of minimizing the potential for harm by reducing waste generation.58 The utilization of stoichiometric reagents in organic synthesis portrays one of the primary sources of waste in the chemical industry, particularly in the production of fine chemicals and pharmaceuticals. Consequently, there is a necessity to replace the practice of using stoichiometric reagents with more atom- and step-economical catalytic alternatives such as biocatalysis.50 The field of catalysis remains a pivotal area of GC, offering atom-economical, selective, and energy-efficient solutions to numerous industrially significant challenges.53 In particular, the field of biocatalysis has developed into an area of significant industrial interest, with its applications spanning the realm of organic synthesis, notably in the enantioselective synthesis of APIs. The catalyst, an enzyme, is composed of readily available renewable resources, is biodegradable, and is essentially non-hazardous and non-toxic. Furthermore, the use of scarce precious metals is circumvented, thereby avoiding the subsequent costs associated with the removal of traces of precious metals from the end products. In addition, enzymatic reactions are typically conducted under mild conditions, frequently without the necessity for activation, protection, and deprotection steps for functional groups.50 The enhanced enzymatic process fulfils a number of GC objectives, including the reduction of solvents, the use of safer reagents and the elimination of superfluous purification stages.58
In order to facilitate sustainable drug discovery and development, AstraZeneca employs the use of biocatalysts to perform some common organic reactions, namely oxidation and amide bond synthesis.59 With regard to oxidation reactions utilizing unspecific peroxygenase, AstraZeneca has demonstrated that the addition of a second protein, designated oxalate oxidase, results in the generation of optimal hydrogen peroxide levels for catalysis. The combination of the two biocatalysts in a ‘one pot’ reaction facilitates an efficient and sustainable late-stage oxidation of a panel of drug molecules without the utilization of metal-based oxidants.60 Furthermore, as part of their research into amide bond synthesis, AstraZeneca developed a biocatalytic step that does not require the use of high temperatures or hazardous solvents. Additionally, the catalysts themselves are sustainably produced and biodegradable.61 The range of chemical reactions that can be conducted by AstraZeneca using biocatalysis is set to expand considerably over the next few years, which will facilitate the exploration of a greater number of sustainable chemical reactions in the context of drug discovery.59
3.3 Electrochemistry and photochemistry
Electrochemistry represents a further synthetic technology that offers the potential to access molecules of considerable structural complexity with a reduced environmental impact, while ensuring safety and robustness.62 Electrochemical methods facilitate redox transformations through electron exchange between electrodes and species in solution, thereby circumventing the necessity for stoichiometric quantities of oxidizing or reducing agents. Consequently, redox steps that involve the use of potentially hazardous or waste-generating reagents during the synthesis of APIs can be replaced with electrochemical procedures.63 The ability to scale up electrochemical reactions through the utilization of flow electrochemical cells has been identified as the most significant advantage of electrochemical methods. This has facilitated the direct commercialization of a proposed synthetic strategy at industrial scales.64 Therefore, electrochemical organic synthesis is frequently regarded as an “inherently green” technology. Nevertheless, it cannot be assumed that electrochemical processing is universally superior to conventional chemical methods. The utilization of substantial quantities of supporting electrolytes in electrochemical reactions, toxic solvents or low substrate concentrations can have a detrimental impact on the environmental sustainability of electrochemical methods. To address these issues, it is essential to perform and to compare a comprehensive quantitative analysis of the green metrics.63
In addition to electrochemistry, photochemistry and photocatalysis have emerged as a significant area of organic synthesis in recent decades, with particular applications in the domain of drug discovery and medicinal chemistry.62 The utilization of light energy by organic molecules and photocatalysts enables the attainment of an excited state, which ultimately culminates in the formation of novel chemical bonds. A considerable number of the recently developed photocatalytic approaches operate under conditions that are highly mild, meaning at room temperature, utilizing visible light, and avoiding the use of toxic and hazardous reagents. Given that light can be viewed as an indefinitely renewable, non-contaminating reagent, and that the majority of photochemical procedures adhere to the tenets of GC, the field of photochemistry presents a promising avenue for achieving more sustainable chemical production.65 Nevertheless, photochemistry as a sustainable technology remains contingent upon overcoming substantial challenges since the utilization of a clean reagent as a photon does not guarantee the attainment of a green process. The selection of the solvent is of significant consequence. Moreover, the necessity for high-intensity artificial light sources, such as a mercury or xenon arc, results in a considerable expenditure of energy due to the suboptimal conversion efficiency.62,66
3.4 Flow chemistry and microreaction technology
The recent acceleration in the development and incorporation of photochemistry in synthesis can be attributed, at least in part, to the advent of flow chemistry.67 Flow chemistry is acknowledged as a pivotal enabling technology for enhancing the efficiency of a chemical process in a multitude of ways, in which chemical reactions are conducted within tubing or microchannels as an alternative to the conventional batch reactor.68,69 The utilization of flow chemistry has become pervasive across the pharmaceutical industry, whereas its application in the context of drug discovery is a relatively recent phenomenon.68 The advantages of utilizing flow chemistry include scalability, safety, speed and reproducibility which are of significant importance for the fulfilment of the ESG criteria.70 Moreover, the flow conditions facilitate more efficient and uniform irradiation of reaction mixtures for photochemistry, while the small dimensions eliminate the need for supporting electrolytes in electrochemistry.71
A related approach to flow chemistry is microreaction technology, which employs microreactors for chemical reactions engineering. The use of microreactors has been demonstrated to be a safe and effective method for the handling of reactions involving unstable intermediates or hazardous reagents, as well as highly exothermic reactions for kilogram-scale synthesis. Moreover, microreactors are capable of transferring heat even under thermal runaway or explosive scenario, and of transitioning from a state of strong heat release to a controllable isothermal operation. This results in a reduction in waste, lower energy consumption, and an increase in the reaction yield achieved in the micro-scale setup, which are all factors that contribute to the life-cycle assessment (LCA) in terms of circularity.70 In comparison to the inherent sustainability potential of chemical production processes, the fabrication of the microreactors and associated equipment represents a relatively minor consideration. It is, however, important to note that the toxicity potential resulting from the production of stainless steel is becoming increasingly significant due to the frequent replacement of microreactors. In certain instances, these toxicity potentials exceed those of the alternative batch process. In light of environmental and economic consequences, it is imperative to devote particular attention to the longevity of micro-structured devices crafted from stainless steel.72
3.5 Circular chemistry and LCA
Research indicates that GC has the potential to accelerate sustainable development by harnessing the synergies between GC and other sustainable strategies, including circular economy (CE).73 Within linear economy, the principles of GC facilitate the optimizations of chemical processes, resulting in the development of more environmentally conscious chemical practices. Consequently, it has established the foundations for an environmentally friendly culture within the chemical discipline. Nevertheless, chemical processes may satisfy the tenets of GC while remaining economically viable, yet ultimately prove unsustainable. Therefore, the transition towards a circular economy requires a reassessment of the criteria that define a sustainable chemical process.
The circular chemistry (CC) approach has the potential to make chemical processes truly circular by expanding the scope of sustainability from process optimization to encompass the entire life cycle of chemical products. In particular, it encourages the efficiency of resources across chemical value chains and emphasizes the necessity to develop innovative chemical reactions for the reuse and recycling of chemicals, thereby facilitating the transition towards a closed-loop, waste-free chemical industry. The objective of CC is to replace the prevailing linear ‘take–make–dispose’ approach with processes that facilitate continuous recycling of materials back into the value chain for reuse. To repurpose waste material into a feedstock, it is crucial to facilitate a recirculation of molecules and materials that guarantee an energy-efficient economy.74 For instance, CO2 can be transformed into an array of other molecules (encompassing methane, alcohols, and amides), which can subsequently be employed for a multitude of applications. However, the conversion process must not necessitate the expenditure of more energy than that offered by the resulting product. In CC, there is also a growing emphasis on the adoption of service-based business models, such as chemical leasing, as a means of promoting the efficiency and longevity of materials.74
While CC offers a conceptual framework for maintaining materials and products within a closed loop, LCA provides a scientific methodology for the quantitative assessment of the environmental impact of these strategies within the chemical and pharmaceutical sector. The integration of LCA into chemical and pharmaceutical manufacturing has the potential to facilitate the identification of environmental impact hotspots and assist decision-makers in the prudent selection of optimized solutions from a range of available options during pharmaceutical and chemical production. In the pharmaceutical industry, LCA has been employed at various stages of the drug manufacturing process. For instance, LCA has been used to identify the most environmentally friendly synthesis route for API, to establish guidelines for the selection of pharmaceutical solvents and enzymes based on their sustainability characteristics, to analyze the environmental impact of the batch platform compared to the continuous platforms in the API synthesis and wet granulation, and to assess the environmental consequences associated with diverse operational conditions in bioreactors.25,75
An exemplar of a circular economy approach within the pharmaceutical industry, incorporating life cycle assessment, can be observed in the case of BASF, whose ChemCycling concept strives to establish a circular plastics economy with chemical recycling. In light of the growing global concern surrounding plastic waste, BASF and their partnerships are committed to addressing this issue through the utilization of pyrolysis technology. This process facilitates the chemical recycling of plastic waste and end-of-life tires, that are not mechanically recycled for technological, economic or ecological reasons, transforming them into a secondary raw material known as pyrolysis oil. The resulting oil will be integrated into BASF’s integrated chemical production network at the outset of the value chain, thereby saving fossil resources through recycled feedstock. A LCA study conducted by Sphera for BASF has determined that the production of plastics using pyrolysis oil under a mass balance approach results in significantly reduced CO₂ emissions in comparison to conventional products manufactured from primary fossil resources.76
4 Drivers and Barriers
The chemical and pharmaceutical sectors play a critical role in global economic development, providing essential products ranging from life-saving medications to key industrial chemicals. However, these sectors are also among the most resource-intensive and environmentally impactful industries. Sustainability is a highly relevant topic for companies in the chemical and pharmaceutical sectors.17,77 As global attention increasingly turns to sustainability, driven by concerns over climate change, resource depletion and environmental degradation, the chemical and pharmaceutical industries face significant pressure to transform their operations.78 This transformation is not only about compliance with stringent environmental regulations79 but also about responding to the growing demands from consumers, investors and governments for more sustainable practices.80,81 Despite the recognized need for sustainability, the path toward it is fraught with challenges. Barriers can be described as factors hampering, delaying or blocking an action aimed at enhancing a firm’s performance.82 At the same time, there are powerful drivers that push these industries towards more sustainable models. Drivers can counteract or overcome barriers, positively influencing the organization and the decision-making process.83
4.1 Firm-external Drivers and Barriers
The chemical and pharmaceutical sectors operate within a complex and highly regulated global environment, where external factors significantly influence the trajectory of sustainability initiatives.84 These firm-external drivers and barriers encompass a range of political, economic, social, technological, and environmental factors that can either accelerate or hinder progress toward sustainability. These external influences set the framework within which companies must navigate their sustainability strategies.
Political drivers and barriers play a crucial role in shaping the sustainability landscape of the chemical and pharmaceutical industries. Regulatory frameworks and government policies not only drive innovation and environmental responsibility but also present significant challenges for companies as they navigate complex compliance requirements and adapt to evolving standards. An example of this political influence is the chemical legislation of the EU, Registration, Evaluation, and Authorization of Chemicals, known by the acronym REACH.85 The REACH regulation is an EU regulation that ensures the safe handling of chemicals. It requires companies to register, evaluate, restrict and authorize extensive data on the chemicals they manufacture or import.86 The introduction of the REACH Regulation in 2013 represented a global paradigm shift in the regulation of chemicals.87 The REACH Regulation brings several benefits that significantly increase sustainability in the chemicals sector. The REACH Regulation offers a high level of protection for human health and the environment. At the same time, it aims to ensure the free circulation of chemicals on the internal market and to promote competitiveness and innovation.88 However, the REACH Regulation can also be a barrier. The size of companies is an important factor in both understanding and complying with the REACH Regulation. The implementation of REACH requires considerable investment in research and administration, especially for small and medium-sized enterprises (SMEs). The effort required to obtain data and comply with the regulations is considerable.87
There are also regulations in the pharmaceutical industry that can hinder sustainable developments. In the pharmaceutical industry, changes to the manufacturing process for APIs become increasingly complex the further the drug is in the development phase. Especially in the later stages of development, such changes are risky and can have a significant impact on the quality and efficacy of the drug. The need to document and approve all changes during the later development phases or after market approval leads to a considerable bureaucratic burden. This slows down the implementation of new, environmentally friendly processes and increases the cost and time required to comply with regulations.89
While political and regulatory factors establish the framework for sustainability, economic factors further shape the chemical industry in its efforts to become more sustainable. The demand for environmentally friendly and sustainable chemicals and environmentally conscious pharmaceutical products is growing. This is driving chemical and pharmaceutical companies to adapt their product lines to meet the demands of an environmentally conscious market.90,91The chemical and pharmaceutical industries, however, are highly competitive and price pressure can prevent companies from investing in more expensive, sustainable technologies. The need to maintain competitive prices can slow down sustainable innovation. Due to fierce competition among suppliers and fewer available resources, small suppliers are in a more difficult position when it comes to adopting sustainable chemistry practices. Many suppliers still rely on waste treatment and disposal rather than waste reduction.92 Furthermore, the volatility of raw material prices is a significant barrier to sustainability in the chemical and pharmaceutical industries. Many essential inputs experience frequent price fluctuations. These fluctuations make long-term planning and investment in sustainable practices particularly challenging.93
Social drivers also play an important role. Growing concern for environmental issues has led to the incorporation of environmental initiatives into the numerous corporate strategies that manufacturing companies employ.94 Key stakeholders can put social pressure on chemical and pharmaceutical companies to adopt more sustainable business practices. Green and environmental non-profit organizations concerned citizens and consumers can voice their concerns about pollution and the safety of chemical manufacturing processes.95,96 The global chemical industry is under pressure to rethink its dependence on crude oil and natural gas imports and to make a carbon transition based on the sustainable use of domestic primary and secondary carbon feedstocks for chemical production. However, it can also be observed that decision-makers can be paralyzed by indecision as they face challenges arising from conflicting policy objectives, the complexity of the regulatory environment and path dependency along institutional and socio-political dimensions.97
There are also technological drivers and barriers to the integration of sustainable practices in the chemical sector. Digitalization enables better data integration and transparency along the entire chemical value chain. By using artificial intelligence (AI) and machine learning, more sustainable chemical processes can be developed and optimized. The chemical industry is increasingly turning to AI to solve complex issues in areas such as process modeling, optimization, control, and fault detection and diagnosis.98 These areas are strongly linked to the industry’s efforts toward environmental, economic, and social sustainability.99 The creation of digital twins of production processes enables companies to virtually simulate and optimize their entire production processes. This supports the development of more sustainable chemical products and processes. Despite advances in digitalization, access to high-quality and complete data is a major challenge. This makes the implementation of sustainable chemical processes more difficult, as incomplete or inaccurate data can lead to suboptimal decisions.100
The chemical industry is a major driver of economic productivity and employment worldwide and ranks among the top three industrial sources of GHG emissions, alongside steel and cement. With global demand for chemical products continuing to rise, there is an urgent need to develop and implement sustainable production methods and to reassess ongoing investments in current, emission-intensive technologies. Given the industry’s significant contribution to greenhouse gas emissions, there is increasing ecological pressure to adopt greener practices. This urgency to reduce emissions acts as a powerful driver for the industry to innovate and explore new technologies that can minimize its environmental footprint.43 However, the industry’s heavy reliance on carbon-based raw materials and primary chemicals, given that most chemical end products contain carbon, presents a significant ecological barrier. The challenge of finding environmentally friendly alternatives to these fundamental raw materials complicates the transition to more sustainable production methods, slowing down the industry’s overall progress towards sustainability.101
4.2 Firm-internal Drivers and Barriers
In today’s business environment, it is widely recognized that sustainability must be integrated into managerial decision-making and corporate strategy development. Despite this, many companies continue to encounter significant operational and organizational challenges as they work toward achieving sustainability transformation.102 In chemical companies, sustainable chemistry innovations must meet both economic and environmental standards. A new product or process must not only be environmentally beneficial but also more profitable without sacrificing quality or effectiveness. For existing products, the cost savings from changes must justify the initial investment.79 Pfizer, for instance, saved millions by improving the synthesis process for sertraline, Zoloft’s active ingredient, which was significant enough to offset the costs of recertifying the drug with the Food and Drug Administration (FDA).48,79,103
Corporate culture in particular plays an important role in the implementation of sustainable strategy measures in the chemical and pharmaceutical sectors. Anchoring sustainability in the corporate culture and management priorities can be seen as a driver of sustainability to enable appropriate change management and day-to-day decision-making. If sustainability is set as a priority for decision-makers, it can be ensured that decisions on the implementation of measures take into account the impact on the entire company and that a company-wide strategy is developed.104 Cultural barriers within the chemical industry can significantly impact innovation. Sectors like consumer products, which constantly adapt to shifting market demands, tend to be highly innovative. In contrast, industries such as pharmaceuticals and bulk chemicals are often more resistant to change, viewing innovation with caution. This reluctance to embrace new approaches can be a major obstacle to adopting green chemistry.79
Many companies continue to face significant challenges when striving for a transformation towards sustainability, especially when it comes to a sustainable supply chain. Green Supply Chain Management (GSCM) has become a strong driver of sustainability in the chemical and pharmaceutical industries.102 Practices and capabilities in sustainable supplier management are recognized as key factors that can enhance the sustainability of both a company and its entire supply chain.105 A company’s image in terms of sustainability depends to a large extent on its supply chain and the sustainability performance of each link in the chain, including suppliers and subcontractors.106 Many companies aim to measure and manage the social and environmental impact of their products throughout their entire global supply chains. Achieving this goal requires manufacturers, as key players in the industry, to carefully select their suppliers, as these suppliers have a substantial influence on the overall environmental and social footprint of the value-adding processes within the manufacturing network.107 Implementing GSCM in the chemical and pharmaceutical industries is often hindered by the inherent complexity of global supply chains. These industries typically rely on a vast network of suppliers and partners, each with its own set of practices, capabilities, and environmental impacts.106,108 Transitioning to greener supply chain practices requires close collaboration across these networks, but not all suppliers may be willing or able to adapt. Finally, this can create significant challenges in aligning environmental goals and maintaining the integrity of the supply chain.109,110
4.3 Best-Practice: Overcoming firm-external and firm-internal Barriers
As leaders in the chemical industry, BASF, DuPont, and Braskem have each developed innovative strategies to overcome the barriers to sustainability. These companies have successfully integrated sustainable practices into their operations, setting benchmarks for others in the industry. BASF is a global leader in the chemical industry, known for its extensive range of products. Among its diverse portfolio, BASF excels in the field of engineering plastics, including polyurethanes, styrene foams, and polyamides. These materials are vital for demanding applications in automotive, medical technology, electronics, and building insulation.111 Committed to sustainability, BASF focuses on improving the performance of its products throughout their entire lifecycle, from production to disposal.76 BASF is recognized as a best practice example for its successful navigation of external political and technological barriers to integrate sustainability into its portfolio. In response to stringent EU regulations, which necessitate substantial investments in research and administration, BASF developed Ecovio, a biodegradable plastic containing polylactic acid (PLA). Through strategic partnerships, such as its collaboration with organizations, governments and industry rivals and the implementation of the Ecovio Eco-Efficiency Compass, BASF was able to meet regulatory requirements while simultaneously developing innovative and environmentally friendly products.80,112
DuPont is a global science and technology company with a strong focus on innovation across multiple industries, including chemicals, materials, and biotechnology.113 DuPont exemplifies best practice by effectively overcoming the political, economic, and technological barriers associated with the introduction of sustainable products. DuPont’s business model focuses on generating sustainable value by both exploring new markets and managing the entire supply chain. The company continually evolves this model through periodic audits conducted by a team of experts in biology, chemistry, materials science, process economics, and product marketing, which identify the top opportunities for renewable raw materials.80 In the face of stringent regulatory requirements within the chemical industry and the need to maintain competitiveness, DuPont developed Bio-PDO (1,3-propanediol) derived from corn sugar and incorporated it into the innovative polymer Sorona.114 Through a strategic partnership with Tate & Lyle and the establishment of a joint venture, DuPont successfully navigated the challenges of backward integration into the agricultural supply chain.80.
Braskem serves as an exemplary case of successfully overcoming external economic and political barriers in the context of sustainability. Leveraging its geographic advantages in Brazil and the existing ethanol infrastructure, the company developed Green PE (bio-based polyethylene) from sugarcane, which acts as a direct substitute for petrochemical polyethylene. Despite the economic challenge of establishing a foothold in a highly competitive market, Braskem effectively communicated the environmental benefits of Green PE through the introduction of the I am Green label, thereby convincing major consumer goods manufacturers such as Coca-Cola and Procter & Gamble.80 The label allows manufacturers to communicate to consumers that products made from Green PE are renewable. This certification enables them to command a premium in the market or to be favored in purchasing decisions at subsequent stages.
BASF, DuPont, and Braskem share several common strategies in overcoming the barriers to sustainability. All three companies have successfully integrated sustainable practices into their operations by leveraging strategic partnerships and innovation. They focus on developing environmentally friendly products that comply with stringent regulatory requirements, while also addressing economic and technological challenges. For instance, BASF’s creation of Ecovio, a biodegradable plastic, and DuPont’s development of Bio-PDO through a joint venture, both demonstrate how collaboration and investment in research can help meet regulatory demands and drive sustainability. Similarly, Braskem’s development of Green PE from sugarcane highlights the importance of communication in overcoming market barriers. Each company’s ability to innovate within the framework of their respective markets and regulatory environments underscores the critical role of strategic partnerships, research, and adaptation in achieving sustainable growth.
References
1 Bhusnure, O., Dongare, R., Gholve, S. & Giram, P. Chemical hazards and safety management in pharmaceutical industry. Journal of pharmacy research 12, 357-369 (2018).
2 Leker, J., Gelhard, C. & Delft, S. v. Business chemistry: How to build and sustain thriving businesses in the chemical industry. First edition edn, (Hoboken, NJ: John Wiley & Sons Ltd., 2018).
3 Verband der Chemischen Industrie. Chemiewirtschaft in Zahlen. 1-179 (2023). https://www.vci.de/vci/downloads-vci/publikation/chiz-historisch/chemiewirtschaft-in-zahlen-2023.pdf.
4 International Council of Chemical Association. The Global Chemical Industry: Catalyzing Growth and Addressing Our World’s Sustainability Challenges. 1-29 (2019). https://icca-chem.org/wp-content/uploads/2020/10/Catalyzing-Growth-and-Addressing-Our-Worlds-Sustainability-Challenges-Report.pdf.
5 American Chemistry Council. Guide to the Business of Chemistry. 1-138 (2023). https://www.americanchemistry.com/chemistry-in-america/news-trends/press-release/2023/acc-publishes-2023-guide-to-the-business-of-chemistry.
6 Bauer, F. & Fuenfschilling, L. Local initiatives and global regimes – Multi-scalar transition dynamics in the chemical industry. Journal of cleaner production 216, 172-183 (2019).
7 Mohan, S. V. & Katakojwala, R. The circular chemistry conceptual framework: A way forward to sustainability in industry 4.0. Current opinion in green and sustainable chemistry 28, 1-9 (2021).
8 Smith, R. 1-29 (Hoboken, NJ, USA: John Wiley & Sons, Inc, Hoboken, NJ, USA, 2005).
9 Marques, C. M., Moniz, S., de Sousa, J. P., Barbosa-Povoa, A. P. & Reklaitis, G. Decision-support challenges in the chemical-pharmaceutical industry: Findings and future research directions. Computers & chemical engineering 134, 1-36 (2020).
10 Kumar, A. et al. When risks need attention: adoption of green supply chain initiatives in the pharmaceutical industry. International journal of production research 57, 3554-3576 (2019).
11 Blum-Kusterer, M. & Hussain, S. S. Innovation and corporate sustainability: An investigation into the process of change in the pharmaceuticals industry. Business strategy and the environment 10, 300-316 (2001).
12 Marques, C. M., Moniz, S., de Sousa, J. P. & Barbosa-Póvoa, A. P. A simulation-optimization approach to integrate process design and planning decisions under technical and market uncertainties: A case from the chemical-pharmaceutical industry. Computers & chemical engineering 106, 796-813 (2017).
13 European Federation of Pharmaceutical Industries and Associations. (European Federation of Pharmaceutical Industries and Associations, 2022).
14 European Commission. (European Federation of Pharmaceutical Industries and Associations, 2023).
15 Agarwal, P., Goyal, A. & Vaishnav, R. Chemical hazards in pharmaceutical industry: An overview. Asian journal of pharmaceutical and clinical research 11, 27-35 (2018).
16 Yang, J. et al. Sustainability performance of global chemical industry based on green total factor productivity. Science of the total environment 830, 1-11 (2022).
17 Lozano, F. J. et al. New perspectives for green and sustainable chemistry and engineering: Approaches from sustainable resource and energy use, management, and transformation. Journal of cleaner production 172, 227-232 (2018).
18 de Faria, D., de Medeiros, J. L. & Araújo, O. Sustainability assessment for the chemical industry: Onwards to integrated system analysis. Journal of cleaner production 278, 1-14 (2021).
19 Isil, O. & Hernke, M. T. The Triple Bottom Line: A Critical Review from a Transdisciplinary Perspective. Business strategy and the environment 26, 1235-1251 (2017).
20 Milanesi, M., Runfola, A. & Guercini, S. Pharmaceutical industry riding the wave of sustainability: Review and opportunities for future research. Journal of cleaner production 261, 1-12 (2020).
21 Makarova, A. S., Jia, X., Kruchina, E. B., Kudryavtseva, E. I. & Kukushkin, I. G. Environmental performance assessment of the chemical industries involved in the Responsible Care®Program: Case study of the Russian Federation. Journal of cleaner production 222, 971-985 (2019).
22 Schmidt, A., Köster, D. & Strube, J. Climate Neutrality Concepts for the German Chemical–Pharmaceutical Industry. Processes 10, 1-17 (2022).
23 International Energy Agency. Direct CO2 emissions from industry in the Net Zero Scenario, 2000-2030, https://www.iea.org/data-and-statistics/charts/direct-co2-emissions-from-industry-in-the-net-zero-scenario-2000-2030-2 (2023).
24 United Nations. Sustainable Development Goal 13, https://sdgs.un.org/goals/goal13 (2024).
25 Chen, Z. et al. Application of Life Cycle Assessment in the pharmaceutical industry: A critical review. Journal of cleaner production 459, 1-16 (2024).
26 Belkhir, L. & Elmeligi, A. Carbon footprint of the global pharmaceutical industry and relative impact of its major players. Journal of cleaner production 214, 185-194 (2019).
27 Lopez, G., Keiner, D., Fasihi, M., Koiranen, T. & Breyer, C. From fossil to green chemicals: sustainable pathways and new carbon feedstocks for the global chemical industry. Energy & environmental science 16, 2879-2299 (2023).
28 Alkaya, E. & Demirer, G. N. Reducing water and energy consumption in chemical industry by sustainable production approach: a pilot study for polyethylene terephthalate production. Journal of cleaner production 99, 119-128 (2015).
29 Li, X. & Hamblin, D. Factors impacting on cleaner production: case studies of Chinese pharmaceutical manufacturers in Tianjin, China. Journal of cleaner production 131, 121-132 (2016).
30 Richie, C. Environmental sustainability and the carbon emissions of pharmaceuticals. Journal of Medical Ethics 48, 334-337 (2022).
31 Environmental Protection Agency. Waste Management by Chemical and Industry, https://www.epa.gov/trinationalanalysis/waste-management-chemical-and-industry (2024).
32 Papafloratos, T., Markidis, I., Kotzaivazoglou, I. & Fragidis, G. Sustainability Material Topics and Materiality Analysis in the Chemical Industry. Sustainability 15, 1-23 (2023).
33 Silvestri, C., Silvestri, L., Forcina, A., Di Bona, G. & Falcone, D. Green chemistry contribution towards more equitable global sustainability and greater circular economy: A systematic literature review. Journal of cleaner production 294, 1-24 (2021).
34 Syaifullah, D. H., Tjahjono, B., McIlhatton, D. & Zagloel, T. Y. M. The impacts of safety on sustainable production performance in the chemical industry: A systematic review of literature and conceptual framework. Journal of cleaner production 366, 1-15 (2022).
35 Reniers, G. & Amyotte, P. Prevention in the chemical and process industries: Future directions. Journal of loss prevention in the process industries 25, 227-231 (2012).
36 Eurostat. Chemicals production and consumption statistics. 1-11 (2023). https://ec.europa.eu/eurostat/statistics-explained/SEPDF/cache/50028.pdf.
37 Holthaus, A. H., Minu. Gender – an essential substance for sustainable chemistry. Journal of Business Chemistry 19, 30-35 (2022).
38 Hemmati, M. B., Anna. Gender and Chemicals. 1-37 (2017). http://gender-chemicals.org/wp-content/uploads/2017/12/2017-12-04-Gender_and_Chemicals_IssuePaper_MSP_Institute.pdf.
39 BASF. BASF-Bericht 2023 Zusammengefasster Lagebericht. 1-190 (2023).
40 European Federation of Pharmaceutical Industries and Associations. Economic and societal footprint of the pharmaceutical industry in Europe. 1-20 (2019). https://www.efpia.eu/media/412939/efpia-economic-societal-footprint-industry-final-report-250619.pdf.
41 Bayer. Geschäftsbericht 2023. 1-283 (2023).
42 Banna, H., Alam, A., Chen, X. H. & Alam, A. W. Energy security and economic stability: The role of inflation and war. Energy economics 126, 106949 (2023).
43 Mallapragada, D. S. et al. Decarbonization of the chemical industry through electrification: Barriers and opportunities. Joule 7, 23-41 (2023).
44 Azad, M. A. K., Munisamy, S., Teng, K. K., Talib, M. B. A. & Saona, P. Productivity Changes of Pharmaceutical Industry in Bangladesh: Does Process Patent Matter? Global business review 19, 1013-1025 (2018).
45 Aquino, R. P., Barile, S., Grasso, A. & Saviano, M. Envisioning smart and sustainable healthcare: 3D Printing technologies for personalized medication. The journal of policy, planning and futures studies 103, 35-50 (2018).
46 Wu, Y. & Tham, J. The impact of environmental regulation, Environment, Social and Government Performance, and technological innovation on enterprise resilience under a green recovery. Heliyon 9, 1-18 (2023).
47 Dechezleprêtre, A. & Sato, M. The Impacts of Environmental Regulations on Competitiveness. Review of environmental economics and policy 11, 183-206 (2017).
48 Manley, J. B., Anastas, P. T. & Cue, B. W. Frontiers in Green Chemistry: meeting the grand challenges for sustainability in R&D and manufacturing. J Clean Prod 16, 743-750 (2008).
49 Zuin, V. G., Eilks, I., Elschami, M. & Kümmerer, K. Education in green chemistry and in sustainable chemistry: perspectives towards sustainability. Green chemistry 23, 1594-1608 (2021).
50 Sheldon, R. A. & Woodley, J. M. Role of Biocatalysis in Sustainable Chemistry. Chem Rev 118, 801-838 (2018).
51 Anastas, P. T., Warner, J. C. & Warner, J. C. Green chemistry : theory and practice. (Oxford University Press, 1998).
52 Anastas, P. & Eghbali, N. Green Chemistry: Principles and Practice. Chem Soc Rev 39, 301-312 (2010).
53 Horváth, I. T. & Anastas, P. T. Innovations and green chemistry. Chem Rev 107, 2169-2173 (2007).
54 Pfizer Inc. Greener Processes, https://www.pfizer.com/about/responsibility/green-journey/greener-processes (2024).
55 Dunn, P. J. The importance of Green Chemistry in Process Research and Development. Chem Soc Rev 41, 1452-1461 (2012).
56 Phan, T. V. T., Gallardo, C. & Mane, J. GREEN MOTION: a new and easy to use green chemistry metric from laboratories to industry. Green Chem 17, 2846-2852 (2015).
57 Kekessie, I. et al. Process Mass Intensity (PMI): A Holistic Analysis of Current Peptide Manufacturing Processes Informs Sustainability in Peptide Synthesis. J Org Chem 89, 4261-4282 (2024).
58 Beach, E. S., Cui, Z. & Anastas, P. T. Green Chemistry: A design framework for sustainability. Energ Environ Sci 2, 1038-1049 (2009).
59 Hayes, M. Performing sustainable chemical reactions with biocatalysts, https://www.astrazeneca.com/what-science-can-do/topics/sustainability/biocatalysis-perform-sustainable-chemical-reactions.html (2023).
60 Romero, E., Johansson, M. J., Cartwright, J., Grogan, G. & Hayes, M. A. Oxalate Oxidase for In Situ H2O2-Generation in Unspecific Peroxygenase-Catalysed Drug Oxyfunctionalisations. Angew Chem Int Edit 61 (2022).
61 Schnepel, C. et al. Thioester-mediated biocatalytic amide bond synthesis with in situ thiol recycling. Nat Catal 6, 89-99 (2023).
62 Cohen, B. et al. Emerging reaction technologies in pharmaceutical development: Challenges and opportunities in electrochemistry, photochemistry, and biocatalysis. Chem Eng Res Des 192, 622-637 (2023).
63 Cantillo, D. Synthesis of active pharmaceutical ingredients using electrochemical methods: keys to improve sustainability. Chem Commun 58, 619-628 (2022).
64 Ghosh, A., Parida, V. K. & Banerjee, D. Challenges and opportunities on sustainable electrochemical transformations: application towards the synthesis of pharmaceuticals and precursors of drug-like molecules. Green Chem 26, 5770-5789 (2024).
65 Buglioni, L., Raymenants, F., Slattery, A., Zondag, S. D. A. & Noël, T. Technological Innovations in Photochemistry for Organic Synthesis: Flow Chemistry, High-Throughput Experimentation, Scale-up, and Photoelectrochemistry. Chem Rev 122, 2752-2906 (2022).
66 Protti, S., Dondi, D., Fagnonia, M. & Albini, A. Assessing photochemistry as a green synthetic method. Carbon-carbon bond forming reactions. Green Chem 11, 239-249 (2009).
67 Guidi, M., Seeberger, P. H. & Gilmore, K. How to approach flow chemistry. Chem Soc Rev 49, 8910-8932 (2020).
68 Bogdan, A. R. & Dombrowski, A. W. Emerging Trends in Flow Chemistry and Applications to the Pharmaceutical Industry. J Med Chem 62, 6422-6468 (2019).
69 Ferlin, F., Lanari, D. & Vaccaro, L. Sustainable flow approaches to active pharmaceutical ingredients. Green Chem 22, 5937-5955 (2020).
70 Hessel, V. et al. Sustainability of flow chemistry and microreaction technology. Green Chem (2024).
71 Plutschack, M. B., Pieber, B., Gilmore, K. & Seeberger, P. H. The Hitchhiker’s Guide to Flow Chemistry. Chem Rev 117, 11796-11893 (2017).
72 Kralisch, D. & Kreisel, G. Assessment of the ecological potential of microreaction technology. Chem Eng Sci 62, 1094-1100 (2007).
73 Loste, N., Chinarro, D., Gomez, M., Roldán, E. & Giner, B. Assessing awareness of green chemistry as a tool for advancing sustainability. Journal of cleaner production 256 (2020).
74 Keijer, T., Bakker, V. & Slootweg, J. C. Circular chemistry to enable a circular economy. Nat Chem 11, 190-195 (2019).
75 Wang, D. P., Cheow, W. S., Amalina, N., Faiezin, M. & Hadinoto, K. Selecting optimal pharmaceutical excipient formulation from life cycle assessment perspectives: A case study on ibuprofen tablet formulations. Journal of cleaner production 292 (2021).
76 BASF SE. ChemCycling®: Creating a circular plastics economy with chemical recycling, https://www.basf.com/global/en/who-we-are/sustainability/we-drive-sustainable-solutions/circular-economy/mass-balance-approach/chemcycling (2024).
77 Mohan, S. V. & Katakojwala, R. The circular chemistry conceptual framework: A way forward to sustainability in industry 4.0. Current Opinion in Green and Sustainable Chemistry 28, 100434 (2021).
78 Matlin, S. A. et al. Material circularity and the role of the chemical sciences as a key enabler of a sustainable post-trash age. Sustainable Chemistry and Pharmacy 17, 100312 (2020).
79 Matus, K. J., Clark, W. C., Anastas, P. T. & Zimmerman, J. B. Barriers to the implementation of green chemistry in the United States. Environmental science & technology 46, 10892-10899 (2012).
80 Iles, A. & Martin, A. N. Expanding bioplastics production: sustainable business innovation in the chemical industry. Journal of cleaner production 45, 38-49 (2013).
81 Bom, S., Jorge, J., Ribeiro, H. M. & Marto, J. A step forward on sustainability in the cosmetics industry: A review. Journal of cleaner production 225, 270-290 (2019).
82 Hueske, A.-K. & Guenther, E. Multilevel barrier and driver analysis to improve sustainability implementation strategies: Towards sustainable operations in institutions of higher education. Journal of cleaner production 291, 125899 (2021).
83 Neri, A., Cagno, E. & Trianni, A. Barriers and drivers for the adoption of industrial sustainability measures in European SMEs: Empirical evidence from chemical and metalworking sectors. Sustainable Production and Consumption 28, 1433-1464 (2021).
84 Veleva, V. R. & Cue Jr, B. W. The role of drivers, barriers, and opportunities of green chemistry adoption in the major world markets. Current Opinion in Green and Sustainable Chemistry 19, 30-36 (2019).
85 Petry, T., Knowles, R. & Meads, R. An analysis of the proposed REACH regulation. Regulatory Toxicology and Pharmacology 44, 24-32 (2006).
86 Ingre-Khans, E., Ågerstrand, M., Rudén, C. & Beronius, A. Improving structure and transparency in reliability evaluations of data under REACH: suggestions for a systematic method. Human and Ecological Risk Assessment: An International Journal 26, 212-241 (2020).
87 Scruggs, C. E., Ortolano, L., Wilson, M. P. & Schwarzman, M. R. Effect of company size on potential for REACH compliance and selection of safer chemicals. Environmental Science & Policy 45, 79-91 (2015).
88 Heselhaus, S. Registration Requirements for Monomer Substances Integrated in Polymers under the REACH-Regulation. European Journal of Risk Regulation 1, 189-193 (2010).
89 Roschangar, F., Sheldon, R. A. & Senanayake, C. H. Overcoming barriers to green chemistry in the pharmaceutical industry–the Green Aspiration Level™ concept. Green Chemistry 17, 752-768 (2015).
90 Lopez, G., Keiner, D., Fasihi, M., Koiranen, T. & Breyer, C. From fossil to green chemicals: sustainable pathways and new carbon feedstocks for the global chemical industry. Energy & Environmental Science 16, 2879-2909 (2023).
91 Milanesi, M., Runfola, A. & Guercini, S. Pharmaceutical industry riding the wave of sustainability: Review and opportunities for future research. Journal of cleaner production 261, 121204 (2020).
92 Sharma, S., Das, J., Braje, W. M., Dash, A. K. & Handa, S. A Glimpse into Green Chemistry Practices in the Pharmaceutical Industry. ChemSusChem 13, 2859-2875 (2020).
93 Laura Juliano, J. P. B., Rebecca Russell, Dimitri Hughes. Gauging the Risks of Raw-Material Volatility, https://www.bcg.com/publications/2022/gauging-risks-of-raw-material-price-volatility (2022).
94 Chaturvedi, U., Sharma, M., Dangayach, G. S. & Sarkar, P. Evolution and adoption of sustainable practices in the pharmaceutical industry: An overview with an Indian perspective. Journal of cleaner production 168, 1358-1369 (2017).
95 Darkow, I.-L. & von der Gracht, H. A. Scenarios for the future of the European process industry – the case of the chemical industry. European Journal of Futures Research 1, 10 (2013).
96 Abdala, E., Oliveira, E. & Cezarino, L. Triple bottom line in Green Supply Chain Management: a chemical industry study. Brazilian Journal of Operations & Production Management 15, 162-172 (2018).
97 Lee, R. P. & Scheibe, A. The politics of a carbon transition: An analysis of political indicators for a transformation in the German chemical industry. Journal of cleaner production 244, 118629 (2020).
98 Zeinab, H., Shokoufe, T. & Mohammad Hosein Eghbal, A. in Artificial Intelligence (ed Aceves-Fernandez Marco Antonio) Ch. 20 (IntechOpen, 2018).
99 Liao, M., Lan, K. & Yao, Y. Sustainability implications of artificial intelligence in the chemical industry: A conceptual framework. Journal of Industrial Ecology 26, 164-182 (2022).
100 Fantke, P. et al. Transition to sustainable chemistry through digitalization. Chem 7, 2866-2882 (2021).
101 Brudermüller, M. in World Economic Forum, Annual meeting.
102 Brömer, J., Brandenburg, M. & Gold, S. Transforming chemical supply chains toward sustainability—A practice-based view. Journal of cleaner production 236, 117701 (2019).
103 Quallich, G. J. Development of the commercial process for Zoloft®/sertraline. Chirality 17, S120-S126 (2005).
104 Bade, C. et al. Sustainability in the pharmaceutical industry—An assessment of sustainability maturity and effects of sustainability measure implementation on supply chain security. Corporate Social Responsibility and Environmental Management 31, 224-242 (2024).
105 Meqdadi, O., Johnsen, T. E. & Johnsen, R. E. The role of power and trust in spreading sustainability initiatives across supply networks: A case study in the bio-chemical industry. Industrial Marketing Management 62, 61-76 (2017).
106 Leppelt, T., Foerstl, K., Reuter, C. & Hartmann, E. Sustainability management beyond organizational boundaries–sustainable supplier relationship management in the chemical industry. Journal of cleaner production 56, 94-102 (2013).
107 Paulraj, A. Understanding the relationships between internal resources and capabilities, sustainable supply management and organizational sustainability. Journal of Supply Chain Management 47, 19-37 (2011).
108 Reuter, C., Foerstl, K., Hartmann, E. & Blome, C. Sustainable global supplier management: the role of dynamic capabilities in achieving competitive advantage. Journal of supply chain management 46, 45-63 (2010).
109 Grimm, J. H., Hofstetter, J. S. & Sarkis, J. Exploring sub-suppliers’ compliance with corporate sustainability standards. Journal of cleaner production 112, 1971-1984 (2016).
110 Coşkun, S. S., Kumru, M. & Kan, N. M. An integrated framework for sustainable supplier development through supplier evaluation based on sustainability indicators. Journal of cleaner production 335, 130287 (2022).
111 Franz, A. W., Buchholz, S., Albach, R. W. & Schmid, R. Towards greener polymers: Trends in the German chemical industry. Green Carbon 2, 33-44 (2024).
112 Daemmrich, A. Co-Innovation of Materials, Standards, and Markets: BASF’s.
113 Rome, A. DuPont and the Limits of Corporate Environmentalism. Business History Review 93, 75-99 (2019).
114 Kurian, J. V. A new polymer platform for the future—Sorona® from corn derived 1, 3-propanediol. Journal of Polymers and the Environment 13, 159-167 (2005).